|
| 
Since its introduction
in 1938, Nylon has become one of the worlds most widely recognized
and utilized engineering grade thermoplastics. Nylons unique combination
of high strength, good toughness, outstanding chemical resistance, and
excellent wear and abrasion resistance have made it the material of
choice for product designs in a multitude of industries. When used to
replace wear grade metals like brass and bronze, no other material provides
the combination of extended wear life, light weight, and low fabricated
part cost of Nylon. Nytef Plastics, Ltd. manufactures UNIPA® Nylon
stock shapes in a wide variety of types and stock shape configurations.
These UNIPA Nylon products fall into the categories of Type 6/6 Extruded
UNIPA Nylons and Type 6 UNIPA M Cast Nylons. While both types of Nylon
are very similar, there are performance and availability differences
between the two grades that should be noted:
UNIPA Type 6/6 Extruded Nylons:
offer
improved toughness
offer
improved flame resistance
are
available in smaller rod diameters (< 2" dia.)
UNIPA M Type 6 Cast
Nylons:
offer
improved wear resistance
are
available in larger rod diameters (up to 13" dia.)
are
available in larger plate sizes (up to 48" x 96")

|
|
|
|
Nytef Plastics utilizes
a proprietary nylon casting process to produce UNIPA M Nylon 6 stock
shapes. This process allows Nylon rods, plates, and tubular bars with
very thick cross sections to be economically produced with uniform physical
properties and minimal internal stress levels. Nytef Plastics
UNIPA M Nylon 6 stock shapes are available in a wide range of grades
including lubricated, heat stabilized, and fiber reinforced products.
UNIPA M Nylon 6 materials are offered in a complete range of round rod,
heavy gauge plate, and tubular bar sizes.
Unipa®
M |
Unfilled
Nylon 6 natural and black
210°F continuous use temperature
|
Unipa®
MLd |
Molybdenum
Disulfide (MoS2) filled Nylon 6
Improved wear resistance
|
Unipa® Mh |
Heat
stabilized Nylon 6
Improved stiffness at elevated temperatures
|
Unipa®
MLo |
Oil
filled Nylon 6
Improved wear resistance
Low coefficient of friction
|
Unipa®
MRg |
Glass
fiber reinforced cast Nylon 6
Improved strength and stiffness |
210° F Continuous Use Temperature
High
Strength and Stiffness
Excellent
Toughness
Superior
Wear and Abrasion Resistance
Outstanding
Resistance to Chemical Attack
Easily
Machined and Fabricated
Food
and Dairy Processing
Paper
Manufacturing
Material Handling
Automotive
Fluid Handling
Textile Production
Electronics Manufacturing
Mining
Construction
Pistons
and Valves
Rollers
and Wheels
Manifolds
Electrical
Components
Food Product
Forming Dies
Bushings
and Bearings
Sheaves
and Pulleys
Gears,
Sprockets, and Star Wheels
Feed and
Timing Screws
Pump Components
Scraper
Blades
Wear Pads
and Wear Strips
|

|
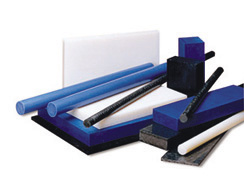 |

|
|
|
|
Nytef
Plastics UNIPA Nylon 6/6 extruded stock shapes are available
in a wide range of grades including both lubricated and fiber
reinforced products. UNIPA Nylon 6/6 materials are offered in a complete
range of extruded round, square, and hex rod, heavy gauge plate, and
tubular bar sizes.
|
|
|
Unipa®
Nylon |
Nylon 6/6, Unfilled Natural and black, natural is inherently
FDA Compliant
|
Unipa®
Ld |
Nylon
6/6, Molybdenum Disulfide (MoS2) Filled Wear resistant, mottled
dark gray color
|
Unipa® Im |
Nylon
6/12, Low Moisture Absorption--High impact resistance
|
Unipa®
Rg |
Nylon
6/6, 30% Glass Fiber Filled High strength and stiffness
|
Unipa®
Rk |
Nylon
6/6, Kevlar® Fiber Filled Highest PV limit of any Nylon,
FDA Compliant, gold color
|
Unipa®
im |
Nylon
6/6, Zytel® ST801 "Super Tough", premium impact
resistance |
210° F Continuous Use Temperature
High
Strength and Stiffness
Excellent
Toughness
Superior
Wear and Abrasion Resistance
Outstanding
Resistance to Chemical Attack
Easily
Machined and Fabricated
Food
and Dairy Processing
Paper
Manufacturing
Material
Handling
Automotive
Fluid
Handling
Textile
Production
Electronics Manufacturing
Mining
Construction
Pistons
and Valves
Rollers
and Wheels
Manifolds
Electrical
Components
Food
Product Forming Dies
Bushings
and Bearings
Sheaves
and Pulleys
Gears,
Sprockets, and Star Wheels
Feed
and Timing Screws
Pump
Components
Scraper
Blades
Wear
Pads and Wear Strips
|

 |
Property |
Test
Method
|
Units
|
UNIPA
M
|
UNIPA
MLd
|
UNIPA
Mh
|
UNIPA
MLo
|
UNIPA
MRg
|
|
|
|
Unfilled
Nylon 6
|
MoS2
Filled Nylon 6
|
Heat
Stabilized Nylon 6
|
Oil
filled Nylon 6
|
30%
Glass Fiber Filled Nylon 6
|
Mechanical
|
Specific
Gravity |
ASTM-D792
|
---
|
1.15
|
1.16
|
1.15
|
1.14
|
1.28
|
Tensile
Strength |
ASTM-D638
|
psi
|
12,000
|
11,500
|
12,000
|
10,000
|
18,000
|
Tensile
Elongation |
ASTM-D638
|
%
|
20-60
|
20-40
|
20-60
|
20-60
|
8
|
Tensile
Modulus of Elasticity |
ASTM-D638
|
psi
|
450,000
|
450,000
|
450,000
|
400,000
|
|
Flexural
Strength |
ASTM-D790
|
psi
|
15,500
|
16,000
|
15,500
|
15,000
|
25,000
|
Flexural
Modulus of Elasticity |
ASTM-D790
|
psi
|
500,000
|
500,000
|
500,000
|
450,000
|
|
Compressive
Strength |
ASTM-D695
|
psi
|
15,000
|
16,000
|
15,000
|
12,500
|
25,000
|
Izod
Notched Impact |
ASTM-D256
|
ft.-lb./in.
|
0.8
|
0.8
|
0.8
|
1.6
|
1.0
|
Rockwell
Hardness |
ASTM-D785
|
M
or R scale
|
M85(R115)
|
M85(R115)
|
M85(R115)
|
M85(R112)
|
M100
|
Thermal |
Coef.
of Linear Thermal Expansion |
ASTM-D696
|
in./in./deg
F
|
4.0
x 10-5
|
4.0
x 10-5
|
4.0 x 10-5
|
5.0
x 10-5
|
1.5 x 10-5 |
Max.
Continuous Use Temp. |
Nytef
std.
|
°F
|
210
|
210
|
210
|
210
|
210
|
Heat
Deflection Temp. @ 264 psi
|
ASTM-D648
|
°F
|
210
|
210
|
210
|
200
|
300
|
Melting
Point |
ASTM-D3418
|
°F
|
430
|
430
|
430
|
430
|
430
|
Electrical |
Dielectric
Strength-Short Term |
ASTM-D149
|
volts/mil
|
400
|
350
|
400
|
400
|
500
|
Dielectric
Constant @ 106 Hz |
ASTM-D150
|
|
3.7
|
3.7
|
3.7
|
3.7
|
3.7
|
Dissipation
Factor @ 60 Hz |
ASTM-D150
|
|
.02
|
|
.02
|
.02
|
.02
|
Volume
Resistivity |
ASTM-D257
|
ohm-cm
|
>1013
|
>1013
|
>1013
|
>1013
|
>1013
|
Miscellaneous |
Water
Absorption/24 hrs. |
ASTM-D570
|
%
weight
|
0.8
|
0.8
|
0.8
|
0.6
|
0.4
|
Water
Absorption @ Saturation |
ASTM-D570
|
%
weight
|
6.0
|
6.0
|
6.0
|
4.0
|
3.5
|
Flammability
|
UL-94
|
|
HB
|
HB
|
HB
|
HB
|
HB
|
Dynamic
Coefficient of Friction
|
|
|
0.26
|
0.25
|
0.26
|
0.14
|
0.33
|
Agency
Approvals |
FDA/USDA
|
|
|
Yes
|
No
|
No
|
No
|
No
|
3-A
Dairy |
|
|
Yes
|
No
|
No
|
No
|
No
|
|
|
 |
Property |
Test
Method
|
Units
|
UNIPA
|
UNIPA
Ld
|
UNIPA
lm
|
UNIPA
im
|
UNIPA
Rg
|
UNIPA
Rk
|
|
|
|
Unfilled
Nylon 6/6
|
MoS2
Filled Nylon 6/6
|
Nylon
6/12
|
Zytel®
ST801
|
30%
Glass Fiber Filled Nylon 6/6
|
Kevlar®
Fiber Filled Nylon 6/6
|
Mechanical
|
Specific
Gravity |
ASTM-D792
|
---
|
1.14
|
1.16
|
1.06
|
1.08
|
1.25
|
1.18
|
Tensile
Strength |
ASTM-D638
|
psi
|
11,500
|
11,800
|
8,000
|
7,500
|
18,300
|
14,750
|
Tensile
Elongation |
ASTM-D638
|
%
|
60
|
50
|
200
|
60
|
4-6
|
4-5
|
Tensile
Modulus of Elasticity |
ASTM-D638
|
psi
|
410,000
|
500,000
|
325,000
|
|
1,200,000
|
|
Flexural
Strength |
ASTM-D790
|
psi
|
14,500
|
15,000
|
14,000
|
|
27,000
|
19,00
|
Flexural
Modulus of Elasticity |
ASTM-D790
|
psi
|
410,000
|
480,000
|
300,000
|
245,000
|
950,000
|
615,000
|
Compressive
Strength |
ASTM-D695
|
psi
|
13,000
|
16,000
|
15,500
|
|
20,000
|
|
Izod
Notched Impact |
ASTM-D256
|
ft.-lb./in.
|
1.4
|
0.8
|
1.2
|
17.0
|
2.3
|
1.0
|
Rockwell
Hardness |
ASTM-D785
|
M
or R scale
|
M80(R121)
|
M85(R115)
|
R108
|
R112
|
M101
|
|
Thermal |
Coef.
of Linear Thermal Expansion |
ASTM-D696
|
in./in./°F
|
4.0
x 10-5
|
4.0
x 10 -5
|
5.0
x 10 -5
|
6.7
x 10 -5
|
1.2
x 10 -5
|
5.0
x 10 -5
|
Max.
Continuous Use Temp. |
Nytef
std.
|
°F
|
210
|
210
|
200
|
210
|
210
|
210
|
Heat
Deflection Temp. @ 264 psi
|
ASTM-D648
|
°F
|
200
|
210
|
149
|
160
|
460
|
450
|
Melting
Point |
ASTM-D3418
|
°F
|
504
|
495
|
423
|
504
|
504
|
504
|
Electrical |
Dielectric
Strength-Short Term |
ASTM-D149
|
volts/mil
|
400
|
350
|
|
|
530
|
350
|
Dielectric Constant @ 60 Hz |
ASTM-D150
|
|
5.0
|
3.7
|
6.0
|
3.2
|
3.5
|
4.0
|
Dielectric
Constant @ 106 Hz |
ASTM-D150
|
|
3.6
|
|
4.0
|
2.9
|
3.7
|
3.4
|
Dissipation
Factor @ 60 Hz |
ASTM-D150
|
|
0.01
|
|
0.015
|
0.01
|
0.014
|
0.01
|
Volume
Resistivity |
ASTM-D257
|
ohm-cm
|
1015
|
1013
|
1013
|
1014
|
1015
|
1015
|
Miscellaneous |
Water
Absorption/24 hrs. |
ASTM-D570
|
%
weight
|
1.2
|
0.7
|
0.25
|
1.2
|
0.7
|
1.0
|
Water
Absorption @ Saturation |
ASTM-D570
|
%
weight
|
8.5
|
6.5
|
3.0
|
6.7
|
5.4
|
8.0
|
Flammability
|
UL-94
|
|
V-2
|
V-2
|
HB
|
HB
|
HB
|
HB
|
Dynamic
Coefficient of Friction
|
|
|
0.25
|
0.23
|
0.30
|
0.29
|
0.31
|
0.30
|
Agency
Approvals |
FDA/USDA
|
|
|
Yes
|
No
|
No
|
No
|
No
|
Yes
|
NSF |
|
|
Yes
|
No
|
No
|
No
|
No
|
No
|
3-A
Dairy |
|
|
Yes
|
No
|
No
|
No
|
No
|
No
|
|
 |
|
 |
Extruded
Nylon |
Diameters
(Rod) |
Thicknesses
(Plate) |
Other
Shapes |
Unipa® |
Nylon
6/6
|
0.250"
- 6.0" |
0.031"
- 2.0" |
Hex
& Square Rod |
Unipa
BK |
Black
Nylon 6/6
|
0.250"
- 4.0" |
0.031"
- 2.0" |
Hex
& Square Rod |
Unipa
Ld |
MoS2
filled Nylon 6/6
|
0.250"
- 4.0" |
0.031"
- 2.0" |
Hex
& Square Rod |
Unipa
Im |
Nylon
6/12
|
0.250"
- 5.0" |
0.031"
- 2.0" |
|
Unipa
Rg |
30%
Glass Fiber Filled Nylon 6/6
|
0.375"
- 6.0" |
--- |
|
Unipa
Rk |
Kevlar®
Fiber Filled Nylon 6/6
|
0.375"
- 8.0" |
0.250"
- 2.0" |
|
Unipa
im |
Zytel®
ST801
|
0.250"
- 4.0" |
0.250"
- 2.0" |
|
Cast
Nylon
|
|
|
|
Unipa
M |
Cast
Nylon 6
|
2.0"
- 13.0" |
0.250"
- 4.0" |
|
Unipa
MLd |
MoS2
filled Cast Nylon 6
|
2.0"
- 13.0" |
0.250"
- 4.0" |
|
Unipa
Mh |
Heat
Stabilized Cast Nylon 6
|
2.0"
- 13.0" |
0.250"
- 4.0" |
|
UnipaMlo |
Oil
Filled Cast Nylon 6
|
2.0"
- 13.0" |
0.250"
- 4.0" |
|
Unipa
MRg |
30%
Glass Fiber Filled Cast Nylon 6
|
2.0"
- 12.0" |
0.375"
- 4.0" |
|
|
|